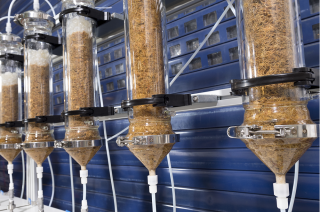
Project
CAPCOM-NL
In the CAPCOM-NL project, a Clean Agro Pellet Commodity was developed to enable the large-scale use of field and process residues for production of electricity, heat, liquid fuels, chemicals and materials.
The project was funded by TKI-BBE and project partners. It is a unique cooperation where the entire supply chain is represented: farmers (Cradle Crops), agro-industry (Palmaceites in Colombia and Raizen in Brazil), technology developers (Viride, Wageningen Food and Biobased Research and TNO), harbour facilities (SmartPort) and possible end users (RWE, AER). The project started in February 2019 and ended in April 2021. WFBR, TNO and Viride have performed the main research tasks.
Project objectives
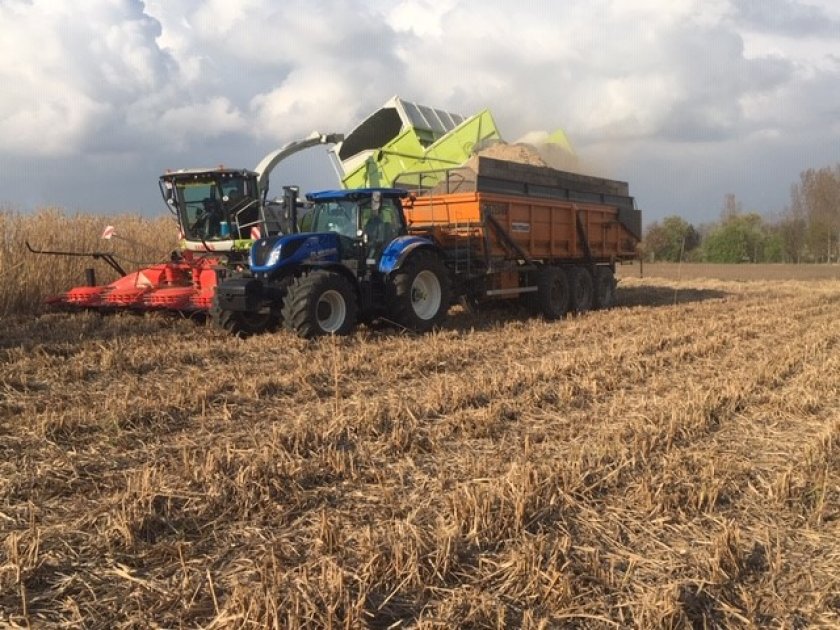

The main focus has been on the best way to connect technologies (counter current mineral extraction, steam explosion and pelleting) to produce a commodity from a range of raw materials (Empty Fruit Bunch, Sugar Cane Bagasse, Sugar Cane Trash, Miscanthus). Such a commodity should be easily transported, transshipped and stored. It should be widely applicable, both as a high quality solid fuel, and as a raw material for production of liquid fuels, chemicals and materials. The commodity has to be sustainable with respect to environmental impact and economy, in the country of origin, during transport as well as in the country of destination. The biocommodity should be able to help to reach the Dutch sustainable energy target (16% sustainable energy in 2023).
Counter Current Extraction (WFBR)
WFBR showed that minerals were successfully removed from the biomass via extraction. Potassium and chlorine were reduced by 90% or more. The minerals are available in the extract (water phase) and may easily be recycled to the field. Single column extractions showed that the characteristic time for mass transfer rate is around 1 to 2 hr. A 3 column counter current setup was applied to produce larger quantities of extracted biomass (20 kg dry matter). This extracted biomass was delivered to Viride for preparation of ‘Green pellets’.
Special pre-treatment process (Viride)
Viride has produced ‘Green pellets’ from raw biomass and from extracted biomass. Steam treated biomass flowed through the pelletizer more smoothly. A reduction of up to 30% energy consumption could be expected at industrial scale by using steam treated biomass compared to raw biomass. The resulting pellets were tested for logistic properties and in combustion and fermentation applications.
Pellet testing (TNO, WFBR, AER)
TNO tested the produced pellets for logistic properties and combustion applications.
The durability of the pellets varied from reasonable to good. The stability of the pellets in humid environments was not satisfactory. Pretreatment reduced the uptake rate of water from the environment delaying deterioration, but in the longer term, increased moulding was seen.
Combustion tests revealed that fouling was highly reduced after extraction of minerals, especially for EFB that had a high initial alkali ash content (Fig 3.). Also the melting behaviour changed from fully flowing to sintered ashes. Emissions (NOx and fines) were better than observed with coal combustion.
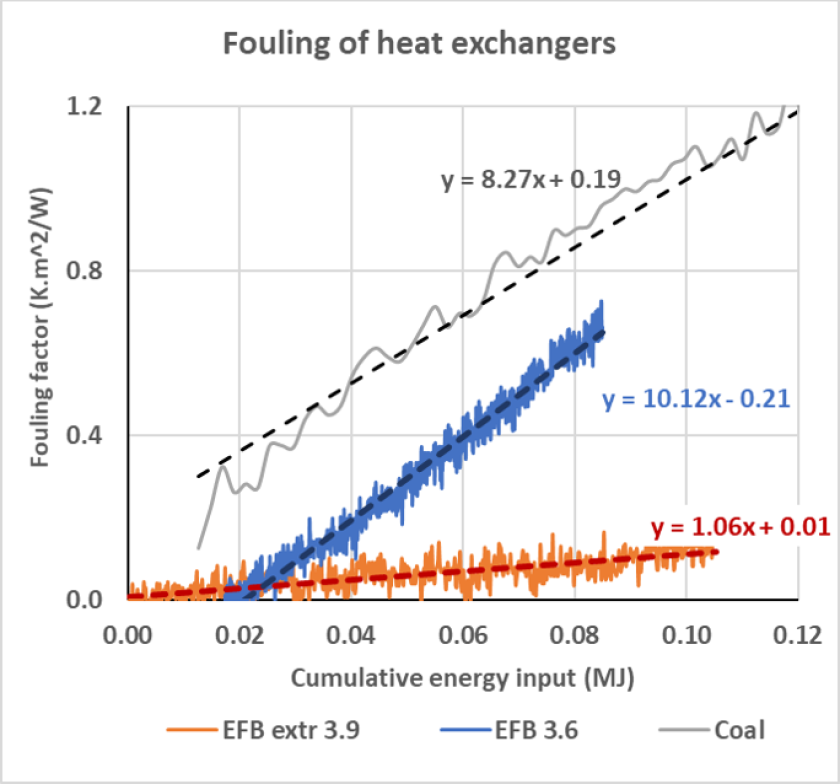
Research at WFBR showed that enzymatic hydrolysis of the pretreated EFB pellets yielded sugar concentrations as expected. The sugar yield after hydrolysis of pretreated SCT and SCB was not sufficient. The sugars in the hydrolysates were easily converted to ethanol (Fig 4.). Some hydrolysates showed a longer initial lag phase, indicating that toxic components may have been formed during pretreatment. In the end, the sugars were readily converted to ethanol, so it seems that this problem can be overcome by adaptation of the yeast.
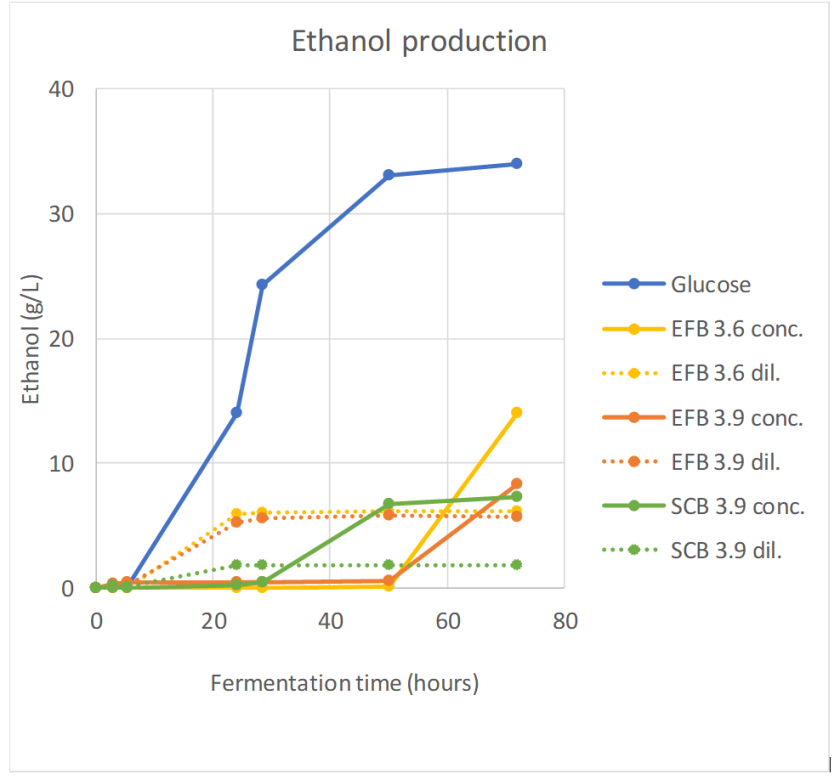
Process design (TNO ,WFBR, Viride, RWE)
A model was built to simulate a full scale counter current simulated moving bed extraction. Based on the experiments a characteristic mass transfer time of 1 hour was used. It was shown that with a 20 heap counter current system, it should be possible to remove over 90% of potassium with 1.2 kg washing water per kg of adsorbed water.
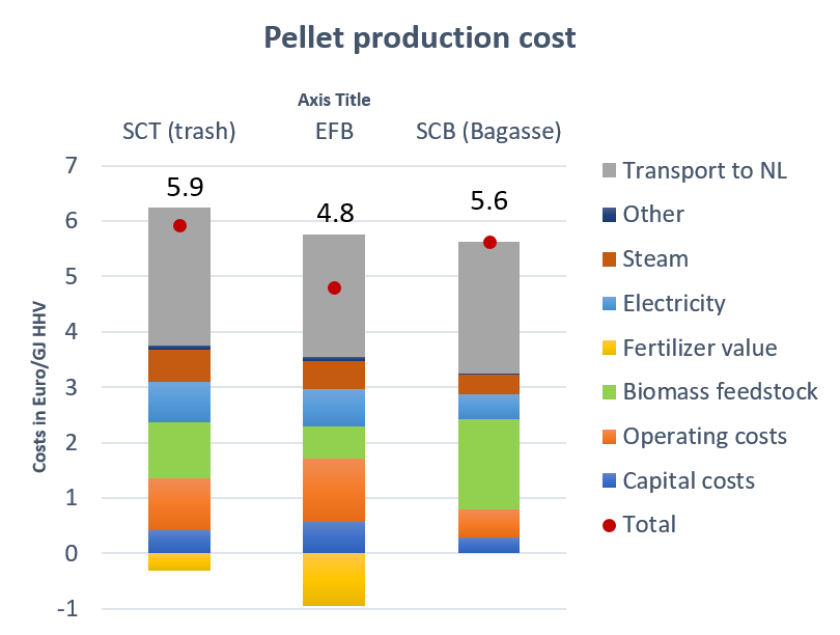
Based on mass and energy balances, the costs for production of pellets were estimated at 4.8-5.9 €/GJ HHV of pellets (Fig 5.) or 5.1–6.3 €/GJ LHV. Especially for EFB the recycling of nutrients in the country of origin leads to a significant reduction of costs.
Sustainabillity analysis (WFBR, TNO, Viride, RWE)
Sustainability analysis showed that the emissions are 90% lower for production of electricity and 70% lower compared to fossil fuels in transport. This is compliant with REDII targets.
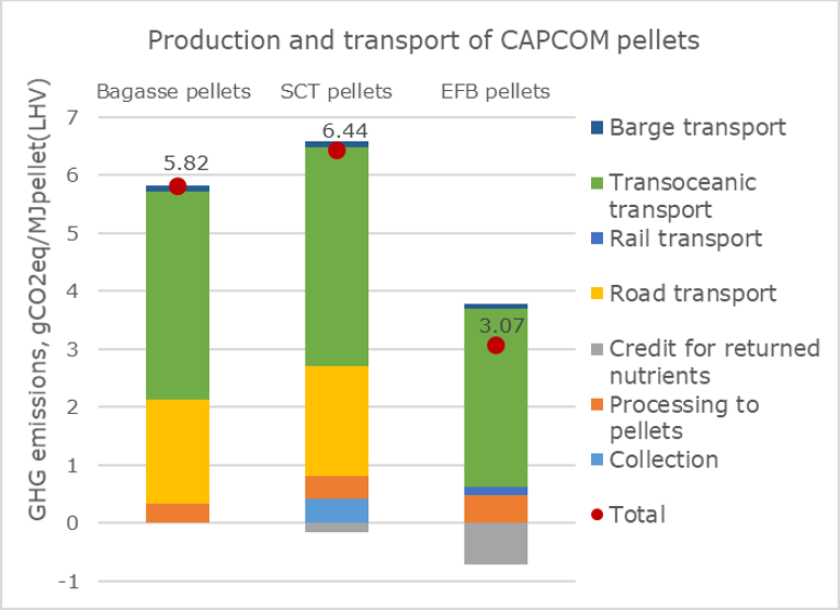
Conclusions
Through extraction, pre-treatment and pelleting, a biocommodity was produced.
After pretreatment, the pelleting process was more smooth and a reduced energy input may be expected. The durability pellets varied from satisfactory until good. Water uptake under humid conditions was reduced, but in the longer term more moulding was observed.
The washed and pretreated pellets are applicable as a fuel in coal fired power plants.
Pellets from pretreated EFB showed sufficient enzymatic hydrolysis to be applicable for ethanol production or other fermentations. During fermentation, a longer lag time was seen. The ethanol yield was good.
The process design showed that the costs of pellets could be around 6 €/GJ.
The sustainability analysis showed that the GHG emissions are low and that savings of >90% can be achieved.